VVT39 - Considering fluid swirl for stationary structures
Test case |
---|
SVTEST280 |
Description
This test case validates the implementation of flow rotation swirl effects on a stationary stator structure under convective thermal coupling conditions, where both the stator and rotor interact thermally through mass-flow ducts.
Geometry
The model consists of two axisymmetric plates—stator (stationary) and rotor (rotating)—connected by a duct representing the mass flow path. The 2D plates length is 200 mm and width is 100 mm. A line between the axisymmetric plates is used to model a duct with mass flow. The distance from the axis of rotation to axisymmetric edge is 100 mm.
Simulation model
A 2D mesh is generated using axisymmetric linear quadrilateral elements that are 10 mm in size. The 1D elements are axisymmetric ducts with a mass flow.
In this model, the stator is on the left and the rotor is on the right.
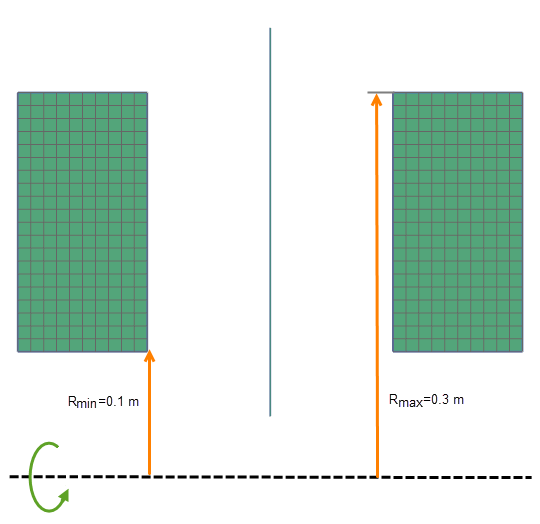
The meshed elements have the following material and physical properties:
- Shell material for the plate: AISI_310_SS
- Mass density: ρ = 7928 kg/m3
- Environmental fluid material: Air
- Mass density: ρ = 1.2041 kg/m3
- Specific heat at constant pressure : Cp = 1004.5 J/kg·K
The following boundary conditions are applied:
-
Convection Coupling type of the Thermal Coupling - Convection simulation object between the edges of both stator and rotor and the duct, with a heat transfer coefficient equal to 0.2 W/(mm2·C), using the following options:
- The rotational effects option is set to Correct for Wall Rotation with a swirl ratio equal to 0.8.
- The Adiabatic Wall Temperature for Heat Transfer Calculations check box is selected. Adiabatic Wall Temperature is set to Automatic
-
The Specify Recovery Factor check box is selected and Recovery Factor is equal to 1.9.
- The Consider Flow Rotation for Stationary Structures check box is selected. Rotation Speed is set to Automatic.
- Duct Fan/Pump type of Duct Flow Boundary Conditions applied to the duct with a mass flow of 0.1 kg/s.
- Temperature constraint applied to the duct elements of 5 °C.
- Temperature constants applied on the external edges of the stator and rotor of 10 °C and 100 °C, respectively.
- Model Subset XY type of the Rotation load applied to the 2D plate on the right with an angular velocity of 2000 rad/s to model the rotor.
This model uses the Simcenter 3D Multiphysics solver.
The following solver options are set:
- Solver = Simcenter 3D Multiphysics
- 2D Solid Option = XY Plane, X Axis
The following solution options are set:
- Solution Control: Element Discretization is set to Finite Element Method in the Thermal Solution Parameters modeling object.
Theory
The heat flow between the surface and fluid is proportional to the temperature difference between the wall surface and the fluid. The reference fluid temperature that results in no net heat flux at the wall is called the adiabatic wall temperature. At this temperature, the wall functions as an adiabatic surface, with no heat transfer occurring across it.
The adiabatic wall temperature Tawstator on the stator side is approximated as:
The adiabatic wall temperature Tawrotor on the rotor side is approximated as:
where:
- Tabs is the total absolute fluid temperature on the wall, which is a defined temperature constraint for the duct.
- Trel is the total relative fluid temperature on the wall.
- RF=Pr1/3 is the recovery factor.
- Vrel = |Vrotor - Vabsfluid| is the relative tangential velocity of the fluid.
- Vϕ = βωr is the absolute tangential velocity, where β is a swirl ratio, ω is a rotor speed, and r is an edge radius.
- Cp is the specific heat at the fluid temperature.
The relationship between Tabs and Trel can be simplified and total relative fluid temperature can be determined as follows:
Results
The following table compares the adiabatic wall temperature of the axisymmetric plate, the total absolute fluid temperature on the stator, and the total relative fluid temperature on the rotor results, predicted by the thermal solver with the calculated theoretical results, measured at 0.1 and 0.3 m from the axis of rotation. The simulation results are in agreement with theoretical values.
Total absolute fluid temperature | Total relative fluid temperature | Adiabatic wall temperature | ||||||||
---|---|---|---|---|---|---|---|---|---|---|
r (m) | Ttheory (°C) | Tsim (°C) | Error (%) | Ttheory (°C) | Tsim (°C) | Error (%) | Ttheory (°C) | Tsim (°C) | Error (%) | |
0.1 | Stator | 5.0 | 5.0 | 0 | 5.0 | 5.0 | 0 | 7.75 | 7.75 | 0 |
Rotor | 5.0 | 5.0 | 0 | 2.13 | 2.13 | 0 | 2.31 | 2.31 | 0 | |
0.3 | Stator | 5.0 | 5.0 | 0 | 5.0 | 5.0 | 0 | 29.76 | 29.76 | 0 |
Rotor | 5.0 | 5.0 | 0 | -20.79 | -20.79 | 0 | -19.26 | -19.25 | 0 |